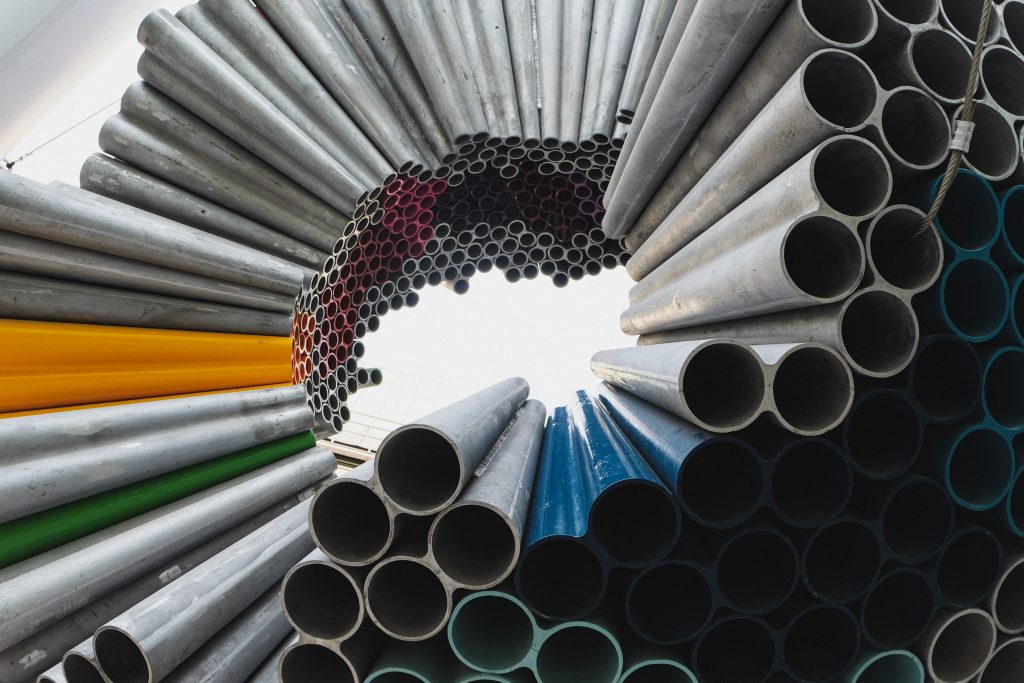
Steel is a permanent material that can be infinitely recycled. The way it is collected and sorted has no impact on its inherent properties. However, these processes do have an impact on the quality and quantity of steel, not only at the classification stage but also during the processing to create a new product.
The best quality is achieved through a single-flow collection, separation, and recycling scenario. In this scenario, if the separation process is inadequate, other materials (ferrous and non-ferrous) may be found in the scrap batch.
Due to its magnetic properties, metal scrap can be easily separated from other materials using one or several magnets in the sorting process. However, this does not guarantee that each batch is free from all types of impurities.
In fact, the amount of other materials in a batch of metal scrap is not only related to the collection source but also to the applied sorting techniques. Depending on the scenarios, the material could be contaminated by various types of non-ferrous and even hazardous ferrous elements when introduced to the furnaces.
It is worth noting that the more complex the collection flow, the more intense the sorting must be. This is because the quality will depend on the accuracy of the sorting. At each stage, additional sorting will be required, and quality checkpoints must be implemented in the process.
The chemistry of materials is crucial.
In his article “Why Scrap Recyclers Need to Know Their Steels,” Dr. Jonathan Margalit argues that scrap yards must ensure that their inventory is accurately identified and properly classified. Their customers will seek the highest level of precision in identifying the metal, as the quality and costs associated with their manufacturing processes depend on it.
Scrap yards use XRF analyzers to identify the various elements contained in metals and classify them appropriately. These analyzers can help determine the composition of the metal and identify “trap elements” (such as copper, nickel, and tin) and positively identify numerous alloys at material transfer points to ensure product quality.
A scrap yard must include in its operations the inspection of all metals entering yards and pits. They must validate them against documentation, quality controls, and the final analysis before materials leave their facilities. Furthermore, the exact chemical composition of the scrap must be determined, including the presence of contaminants or hazardous elements, to ensure quality, safety, and regulatory compliance. The higher the integrity of the scrap received by the customer, the greater the reputation of the supplier.
Implement a predictive model for chemical profile classification.
SCRAPYARD® allows you to integrate material chemistry to certify the received scrap. Then, it performs AI-based analysis to classify it by chemical profile, scrap type, suppliers, etc. This will allow you to learn from your process, optimize the basket load, and rate the quality of your suppliers.
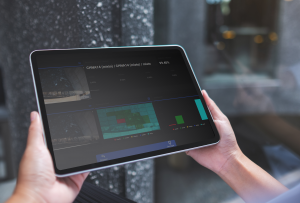
As mentioned at the beginning of this article, technology is a reliable ally in effectively classifying recycled materials entering production processes. SCRAPYARD® features modules specifically designed to ensure the safety, quality, and efficiency of metal scrap recycling processes.
Eliminate discrepancies and reduce operator interaction with the results of scrap management and classification stages by using SCRAPYARD®. It provides an automatic process for recording data in the system without manipulating information, delivering records, images, and videos of the scrap that has just entered the plant.
Achieve these impacts with SCRAPYARD®, the only comprehensive solution in the market for the management and classification of metal scrap.