SUCCESS STORIES – IT SOLUTIONS
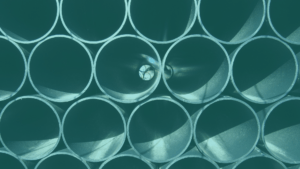
Cases
AUTOMATION OF TUBE FINISHING LINE
SUCCESS STORIES– INDUSTRIAL AUTOMATION THE PROBLEM Our client, an international company specializing in the manufacturing of seamless pipes primarily for the oil market, requires an